gas/oil /water pipeline Puf Pre-Insulated Pipe PE shell casing
plastic Machinery
Technical Prameters:
| PE-365/760 | PE-420/960 | PE-850/1372 | PE-960/1680 |
Main extruder | SJ-90/33 | SJ-90/33 | SJ-120/33 | SJ-150/33 |
Pipe diameter (mm) | Φ365-960 | Φ420-960 | Φ850-1372 | Φ960-1680 |
capacity (kg/h) | 550-700 | 550-700 | 700-900 | 800-1200 |
Installed power (kw) | 360 | 380 | 440 | 580 |
Length (m) | 35 | 36 | 40 | 48 |
The core technology of Huastar PE960-1880 insulation pipe
production line is at the leading level in China, and a number of
innovation points and design concepts have filled the gaps in
China, among which four core technologies such as solid-liquid
phase separation screw, spiral diverter head, DCL human-machine
dialogue technology, and real box external manipulator technology
are the first or first applied in the industry. This product is
also the only domestic production line capable of manufacturing
1880mm large diameter insulation pipe.

Design a traction machine with friction as the core, replacing the
old traction machine with larger gripping force to pull the pipe,
avoiding the deformation of the thin-wall pipe in the processing,
eliminating the secondary processing process.
Using ring hydraulic planetary cutting machine, the incision
section is neat, and the processing is in place at one time,
replacing the manual cutting with hand saw.
The whole line uses PLC artificial AI control to realize automatic
production, remote monitoring and automatic printing, participating
in intelligent production management, production quantitative
digital extraction, control of qualified rate waste products in the
production process, etc., with small space occupation and minimal
labor, each line only needs 2 people.
Automatic collection and treatment of exhaust gas, no need to add
post-exhaust gas purification equipment, in the head part of the
hole, equipped with exhaust gas collection system. Ensure that
there is no exhaust gas emission at the end of the pipe incision,
reduce the investment of exhaust gas purification equipment, and
refuse air pollution.

The production steps of insulation layer are as follows: firstly,
the steel pipe is penetrated into the high-density polyethylene
outer protection pipe to form a casing structure, and the supports
are evenly arranged in the annular space between the steel pipe and
the high-density polyethylene outer protection pipe, and the two
ends are sealed by flanges; secondly, the casing is hoisted on the
foaming platform, and the polyurethane foaming material is injected
into the casing by high-pressure foaming machine; finally, the
polyurethane material is foamed After curing, the sealing structure
at both ends is removed to complete the production process of the
insulation layer.
Rigidity due to the presence of strong ties between the steel pipe
layer polyurethane insulation and jacket pipe and provides pre-shot
blast or blast cleaning the surface of the steel pipe, optimum
performance polyurethane insulation, corona surface of polyethylene
pipe shell.
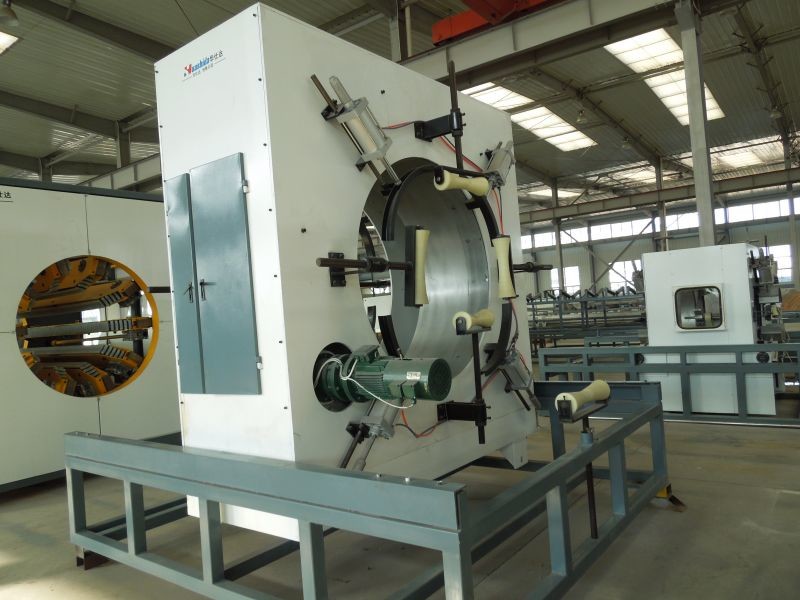
gas/oil /water pipeline Puf Pre-Insulated Pipe PE shell casing
plastic Machinery Advantages:
Significantly increases the reliability of the pipeline in the PUF
insulation system operational availability of remote condition
monitoring PUF insulation, which allows to detect and repair
leaking coolant, preventing accidents typical for thermal networks
of other designs.
Highly cost-effective use of pipelines in the foam insulation
define the following parameters:
Simplifying the construction, maintenance and repair;
Increased service life of 30-40 years (traditional types of
pipelines - 5-10 years);
Reduction of heat losses to 8% (traditional types of pipelines -
30-40%);
Reducing capital costs by 15-20% (not required construction of
concrete channels and chambers for valves);
Reduced operating costs by 9 times;
Reduction in repair costs 3 times.